Using Work Orders to Streamline Equipment Maintenance
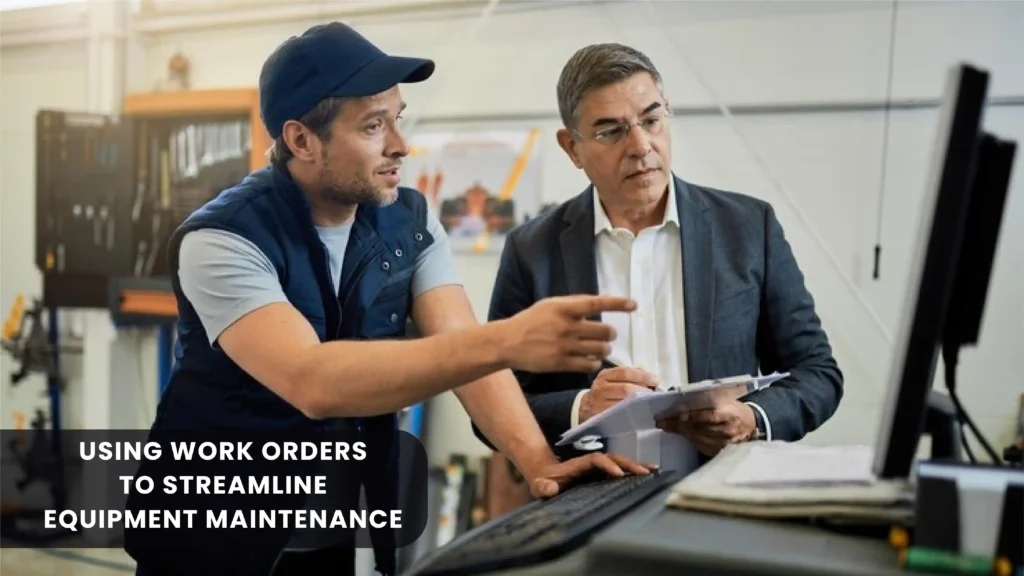

For users of the INTERAC Equipment Cost system, we want to be sure that you are aware that it includes an integrated work order system to help manage equipment maintenance. It is quick and easy to generate work orders for the shop which outline the service to be performed, the anticipated parts required, and even the mechanic assigned to do the work.
Description of Work
The work order header includes a free form description which allows you to clearly define the maintenance to be performed.
Repair Parts
Equipment Work Orders can utilize items from either the purchased parts file in Equipment Cost, or the INTERAC Inventory system. This makes it easy to select the appropriate parts for the maintenance and it prints them on the work order to avoid any confusion.
Labor
You can pre-assign a mechanic or service technician to perform the maintenance and estimate the hours required to complete the work. The system will calculate the labor cost based on the hours times the rate.
Miscellaneous Items
Work orders will also accommodate miscellaneous items for things other than parts and labor.
These work orders can be marked up by the service mechanic and then used to enter the maintenance updates into Equipment Cost. They can be linked to that piece of equipment in the Document Management System, making the documentation readily available in both Equipment Cost and Equipment Manager.
If you are not already taking advantage of this feature, we would encourage you to give it a try. It could improve the accuracy of your maintenance reporting and help to streamline the process at the same time.